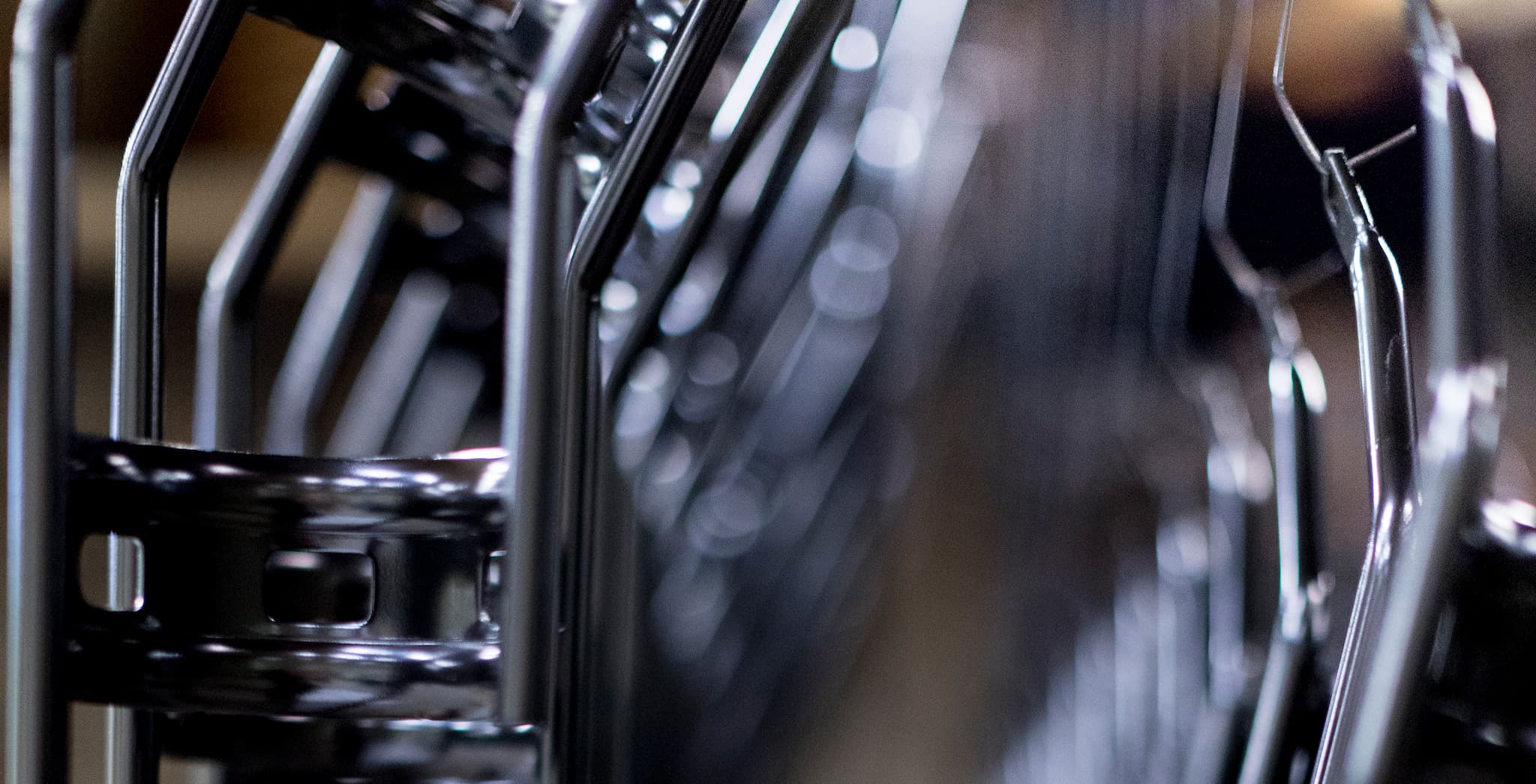
Our areas of expertise
Our employees’ technical skills and expertise in pipe bending, end forming and welding of pipe components creates security and simplicity for you as a customer. Click here to read more about our areas of expertise and how we can help you.
Technical expertise that makes a difference
For us, it’s all about delivering high-quality solutions with great service that makes our customers feel confident in working with us. What primarily makes us a a leading supplier are our employees, who possess high technical expertise and are
are experts in tube bending, end forming and welding of tube components for the automotive and engineering industries. Together with our state-of-the-art equipment, our high customer focus and long experience, we can deliver world-class solutions to customers around the world.
Working with Proton Engineering should be easy and we are committed to listening to your needs
– and do what it takes to make your dream a reality!
Below you can read more about our services and what we offer.
Pipe bending & end forming
We have extensive experience in advanced tube bending in materials such as steel, stainless steel and aluminium. We bend tubes and profiles in various materials and shapes, including welded and straight tubes, as well as profiles such as round tubes, square tubes and even elliptical tubes. Our CNC-controlled bending machines handle dimensions from 6 to 150 mm, with or without mandrel, and create both fixed and free radii.
In our automated production, we use advanced production cells for tube bending, profile bending, end forming and hole making in dimensions from 6 to 63 mm. By using seam tracking, we ensure precise bending at every stage.
Our automated cells also have the capacity for stud welding, which facilitates assembly for you as a customer.
End forming is another important part of our process. This is done either as part of our automated cells or as a separate operation. End moulding allows for different assembly solutions, such as preparing the pipe for hose assembly or creating fasteners. It is a complete process that provides flexibility in final assembly.
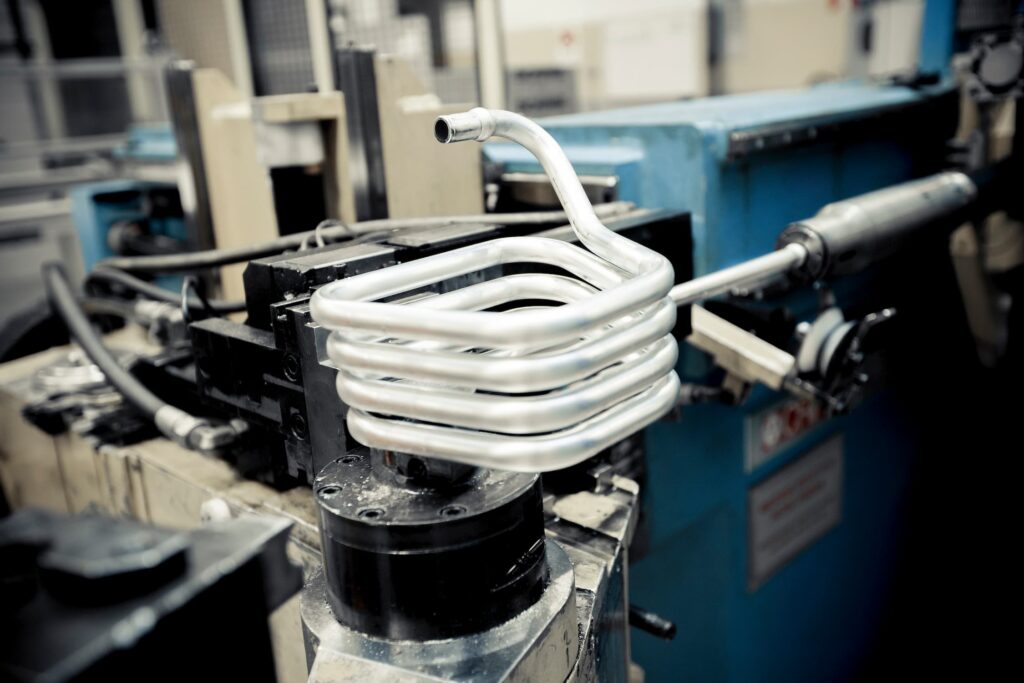
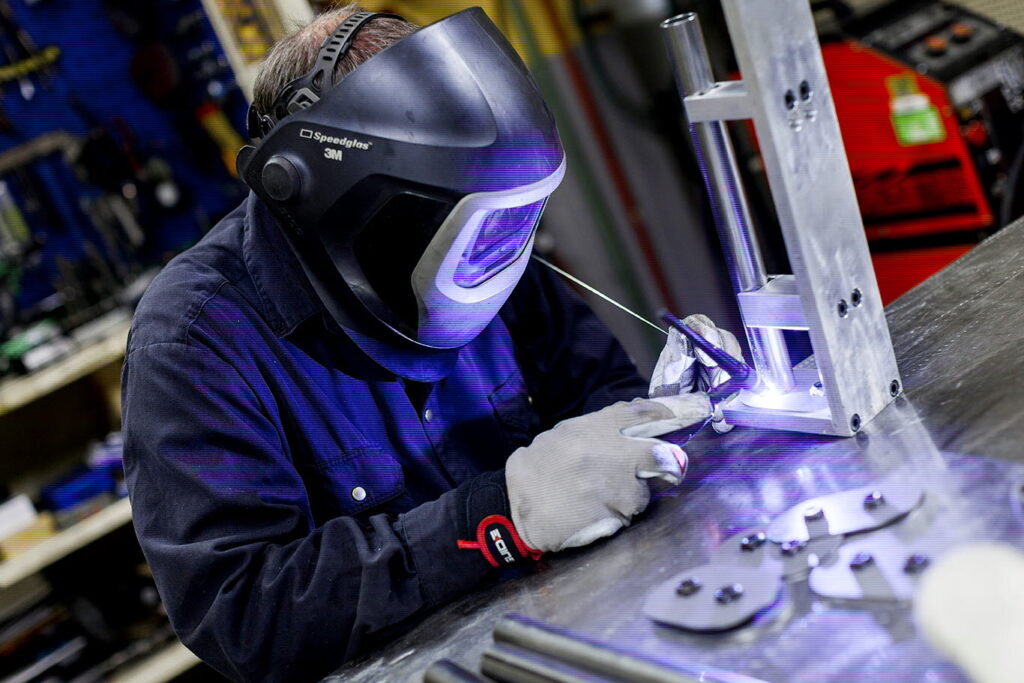
Welding
We are experts in welding, with both robotic and manual welding of complex sheet metal, profile and pipe structures for leading automotive and engineering industries. We use MIG/MAG and TIG welding in steel, stainless steel and aluminium. Our robotic welding with advanced CMT technology produces high-quality and virtually spatter-free welded joints, minimising the need for rework.
We have several robotic cells for welding up to 2.5 x 1 metre and weight up to 150 kg per side. In addition, we use spot welding to create strong joints on sheet metal, especially in steel up to 3 mm thick, aluminium and stainless steel.
In sheet metal processing, we use laser cutting to create details for our welded structures. Our 4 kW fibre laser can handle material thicknesses up to 20 mm with nitrogen for clean cuts, which is perfect for painting. For any machining after laser cutting we use an 80 tonne edgebander.
When brazing is better than welding, we offer induction brazing for steel and stainless steel. Induction brazing provides consistent, stable and high-quality results with minimal risk of weak joints or overheating.
Our experienced staff are licensed according to ISO 9606-1 and work with WPS (Welding Procedure Specification) to ensure standardised quality. We take care of the entire manufacturing flow from tube bending to welding and sheet metal processing, with a focus on delivering high-performance and cost-effective solutions to our customers.
Assembly
We offer assembly of various components into complete products that are delivered to customers in the automotive and engineering industries. Through our two production units we have assembly capacity both in Sweden and in Lithuania.
We take care of the entire assembly process to simplify manufacturing and can deliver directly to our customers’ facilities worldwide. Our assembly includes various tests to ensure that all customer requirements are met, such as cleanliness testing and tightness checks.
We perform assembly of composite parts with high quality and efficiency. We use use advanced techniques, such as assembly without welding to avoid risks such as burn-through. When specialised machinery is needed for assembly, we work closely
with various automation companies to ensure both cost-effectivenesscost-effectiveness and a good, high-quality end result.
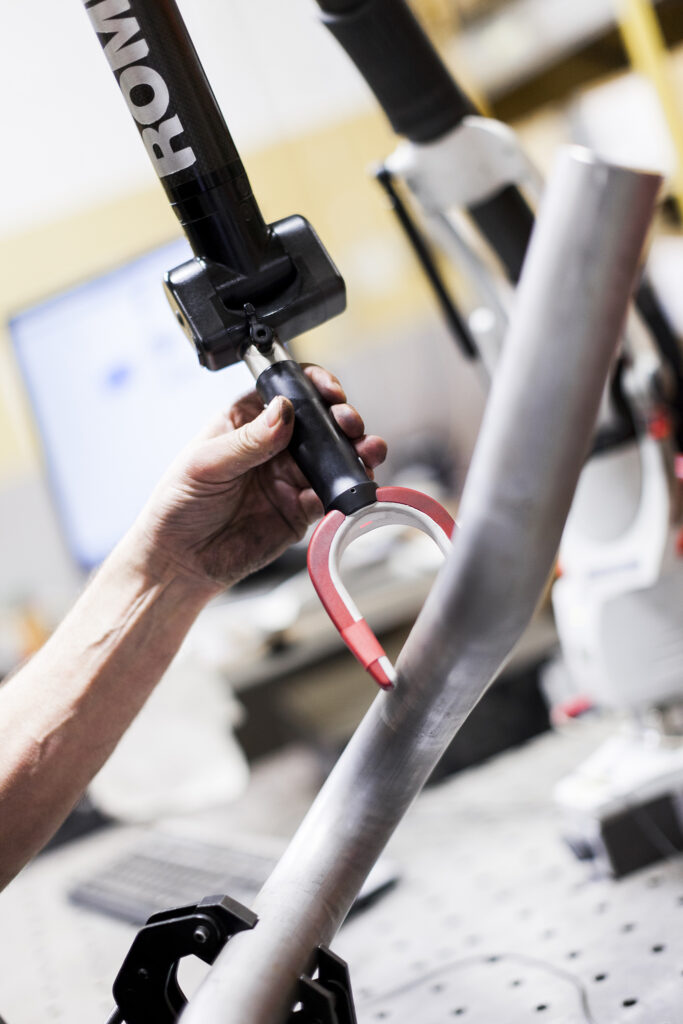
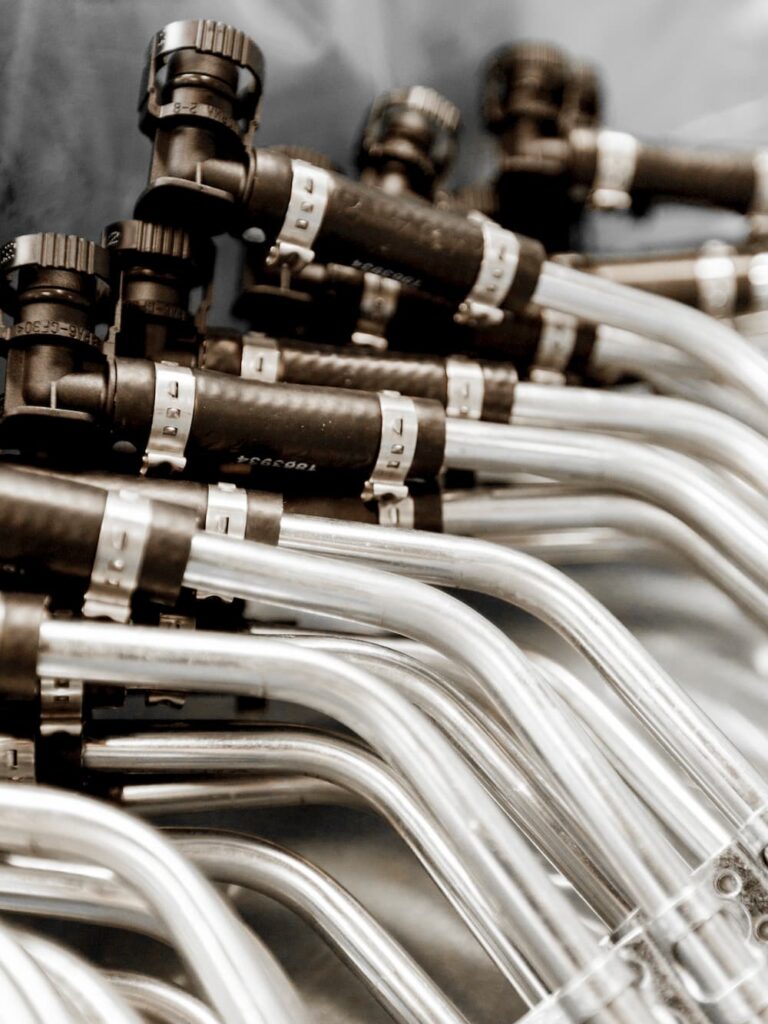
Other services
We specialise in the design and manufacture of welding, assembly and control fixtures and tools for the automotive and engineering industries. We have advanced eccentric and hydraulic presses with a capacity of up to 160 tonnes for flattening and punching.
Our experienced employees in the tool and fixture department have long experience in the design, development and manufacture of different types of fixtures and tools. Together with our customers, we create customised solutions to efficiently manufacture high quality products.
Examples of fixtures include welding fixtures for both robotic and manual welding, inspection fixtures, leak detection fixtures, assembly fixtures and machining fixtures. We also manufacture various tools for bending, end forming and pressing according to customer needs.
Together with our subcontractors, we also offer surface treatment according to customer requirements and deliver finished products directly to the customer to ensure efficient and sustainable production flows.
Do you want to know more?
Want to know more about how we can help you, or have other questions?